

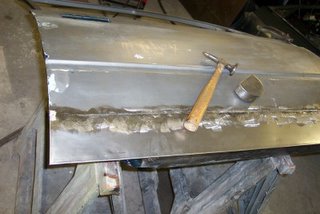




More about the Biturbo
We have repaired a major amount of rust. When faced with extensive corrosion a good approach is to obtain a donor car. Rather than fabricating complicated panels and structural assemblies from scratch, it is almost always easier and less expensive to obtain used parts from another vehicle. Granted this is not always possible but in the case of our Biturbo we found a rust-free car that was being parted-out. We specified where to make the cuts so that we had plenty of material to work with. In this way we were able to replace large portions of the floor pan and adjoining rocker/sill assembly in complete sections.
The first step is to get the undercoating and seam sealer out of the way. Scrapers and propane torches work well but a great (although pricey) tool I like is the rotary wire brush available from several manufacturers. The hook shaped wire bristles are very aggressive (and re-sharpenable). I prefer to clean more than what might seem needed. Later on, during the welding and hammering stage, I have less smoke and drippy undercoating to deal with. Once the pieces are cleaned up we went ahead planning our splices.
We used existing bends, especially in the floor pans to help plan the cut lines. Also, we took advantage of the structure to help make the job easier. So instead of cutting the floor pan just anywhere, we spliced right over an existing stiffener. This gave us a readily identifiable place to cut as well as resulting in a stronger seam.
As you can see, we replaced a large section of the left side floor pan and inner rocker. ‘How did this much damage occur?’ you may be wondering. It seems to us that a few small rust holes opened up high on the firewall. This allowed water to run inside the car which was combined with a long period of outside storage (never a good idea). And of course ‘rust never sleeps’. Quietly doing its job 24/7, happily providing work for those of us foolish enough to go into the auto restoration business. That and, of course the fact that the car was built by the Italians. It must not rain in Italy.
After the welding and grinding were done we applied two-part urethane seam sealer liberally. I’ll back-up here and mention that inside surfaces were painted with either rust encapsulator or zinc-rich weld thru primer prior to welding. We anticipate a tough life for this car so the floor pans and inner sills got two coats of ‘Rustoleum’ enamel. Not historically correct but then this is not to be a museum piece.
The bottoms sections of all fours doors were re-skinned. In addition, I had to fabricate the bottoms of the door frames. Is there polyester filler (bondo) on these doors? Yes. Modern fillers mixed in the correct proportions and applied and used properly, that is, among other things; nothing thicker than 1/8 inch and never forming an edge, will last practically forever. Metal finishing a panel to near perfection takes a lot of time, time that may not be warranted.
After all the body work is flat and sanded with 180 grit, the car gets washed with wax/grease remover followed by a coat of self-etching primer and three coats of surfacer. That’s where we are now. The car has been allowed to dry for over a week so the next step is dry blocking the surfacer with 220 grit on the longest sanding boards practical
No comments:
Post a Comment